1. Introduction
1.1 Purpose - Component Details
The "Component Details"-tab in the maintenance system serves as a comprehensive repository of essential information related to each individual compontents within the "Maintenance"-module.
This tab is designed to provide maintenance personnel and stakeholders with a centralized and easily accessible source of detailed specifications, operational history, and relevant documentation for each component.
Example of Component Details for Main Engine.
1.2 Key Features - Component Details
1.2.1 Schematic Image
Ability to upload a visual representation of the component's schematic or diagram.
1.2.2 SFI Code/Component Name
Each component is identified by its SFI code and name. For instance, a typical entry would be:
SFI Code - 601.01
Component Name - Main Engine
1.2.3 Technical Specifications
Input comprehensive technical specifications, including model, serial number, location, and maker.
1.2.4 Component Settings
In the "Component Settings"-section you can adjust, and enable certain options which is integrated in various parts of the system:
Critical Component - Marks the Component as a "Critical Component". This will be reflected in the Maintenance table overview.
Class Component - Assign the Component an Class ID. This will be reflected in the Mainteance table overview.
Spare Component - Under Development.
2. Getting started

It's important to note that this function depends on the configuration of the maintenance SFI system and how the menus are designated as either COMPONENT or COMPONENT GROUP.
- The COMPONENT GROUP functions solely as a parent menu for the COMPONENT, and offers limited options for inputting any component details.
- A COMPONENT can not be created in the system without a specific parent menu (COMPONENT GROUP), but each COMPONENT will offer numerous options for inputting detailed information about the specific component.
2.1 Accessing the Component Details
Each Component and Component Group in the Maintenance-module has these following tabs: Component History, Component Details.
To access this component information, go to the "Maintenance"-module. Follow the current established structure to locate and navigate to the specific component for which you want more detailed information.
Access "Maintenance"-module.
Locate the Component "601 Main Diesel Engine" by navigating through the parent menus.
Once you find the correct component within the "Maintenance" module, you can access its detailed information through the "Component Details".
2.2 User Interface Overview
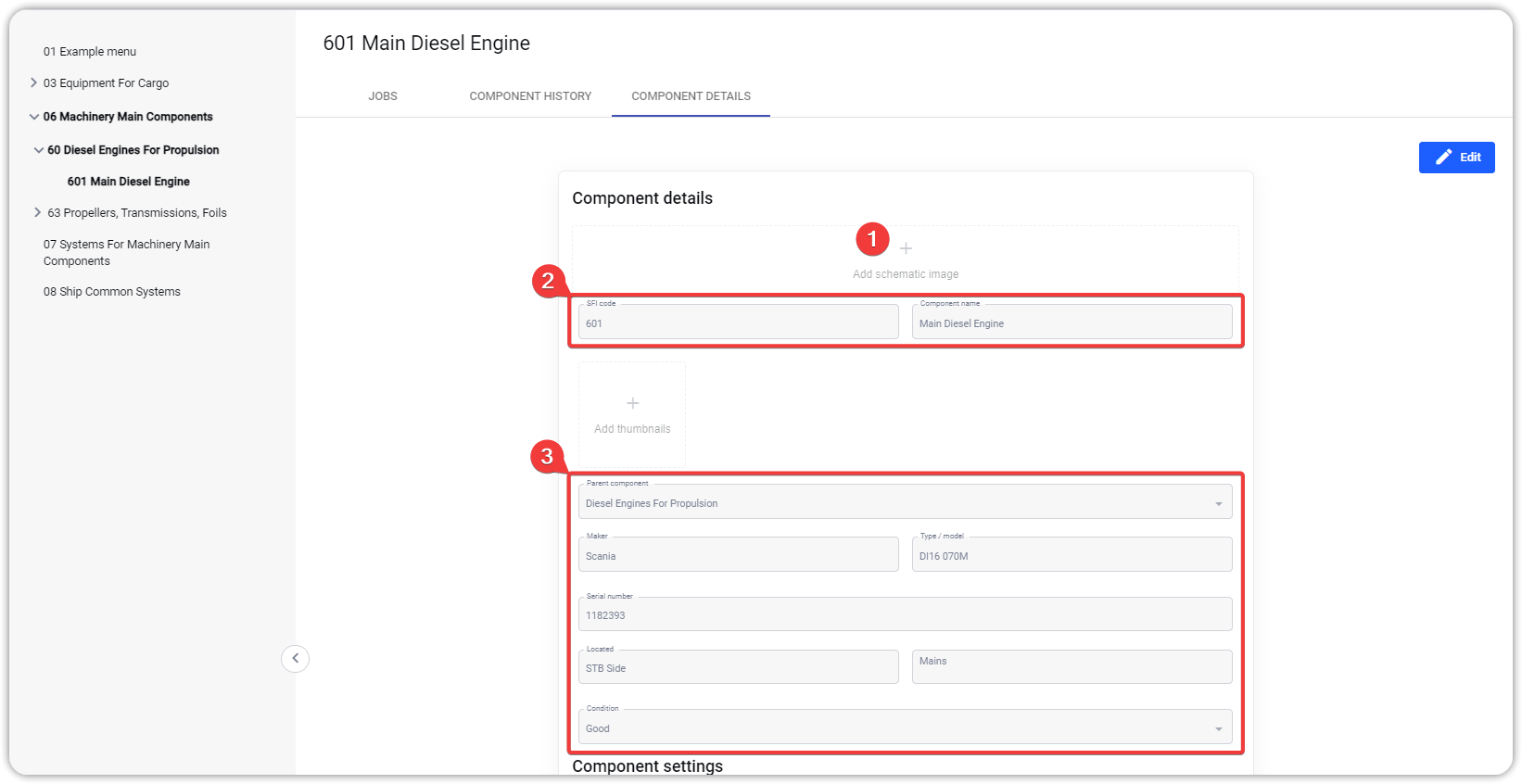

2.2.1 Schematic Image
Ability to upload a visual representation of the component's schematic or diagram.
2.2.2 SFI Code/Component Name
Each component is identified by its SFI code and name. For instance, a typical entry would be:
SFI Code - 601.01
Component Name - Main Engine
2.2.3 Technical Specifications
Input comprehensive technical specifications, including model, serial number, location, and maker.
2.2.4 Component Settings
In the "Component Settings"-section you can adjust, and enable certain options which is integrated in various parts of the system:
Critical Component - Marks the Component as a "Critical Component". This will be reflected in the Maintenance table overview.
Class Component - Assign the Component an Class ID. This will be reflected in the Maintenance table overview.
Spare Component - Under Development.
2.3 Configuration
To configure information in the datafields, click on the "Edit"-button located in the top right corner:
Click the "Edit"-button.
After clicking "Edit" the fields will be open for any changes.
Related Articles
8.3 Tagging components as critical
User Privileges In order to tag a component as critical, you first need the necessary Job Position Privileges to access the Admin Settings in CCOM X. Contact the person who is technical responsible in your company, or CCOM Support, to have this ...
Maintenance Module - Admin settings
1 Introduction 1.1 Purpose The system's maintenance module must be configured correctly before it can be used effectively. Within the “Maintenance” section, the user must populate several menus with correct data. These menus are: Job Types Components ...
8.2 Performing/editing a maintenance task
Perform Users typically start by accessing the Maintenance module within the system. Within the module, users can view a list of all available maintenance jobs. This list provides an overview of tasks that need attention. Users choose a specific ...
Certificate-module description
Overview The table overview offers an organized overview of all certificates within the selected folder, including any sub-folders (if they exist). The columns in this table provide a concise summary containing essantial details for each registered ...
Storage
Overview The table overview in the Storage-items module offers a structured representation of all stored items. It features columns that define various attributes such as article numbers, product names, components, quantities, quantity types, and ...